Unlocking the Power of Welding WPS: Strategies for Efficiency and Safety in Fabrication
In the realm of fabrication, Welding Procedure Specifications (WPS) stand as the backbone of welding procedures, determining the essential actions for attaining both performance and safety and security in the manufacture procedure. Understanding the details of WPS is vital to harnessing its full potential, yet numerous organizations battle to open the real power that lies within these files (welding WPS). By delving into the methods that enhance welding WPS, a world of enhanced performance and increased safety waits for those eager to discover the subtleties of this crucial element of fabrication

Value of Welding WPS
The significance of Welding Procedure Requirements (WPS) in the manufacture sector can not be overemphasized. WPS serve as a vital roadmap that lays out the needed steps to make certain welds are done regularly and correctly. By specifying vital parameters such as welding procedures, materials, joint layouts, preheat temperatures, interpass temperatures, filler steels, and post-weld heat therapy requirements, WPS supply a standardized strategy to welding that improves efficiency, quality, and security in manufacture processes.
Adherence to WPS aids in accomplishing harmony in weld top quality, minimizing the likelihood of flaws or structural failures. This standardization additionally helps with conformity with industry guidelines and codes, making sure that produced structures satisfy the required safety criteria. Furthermore, WPS documents enables welders to reproduce effective welding procedures, resulting in regular outcomes across different projects.
Essentially, the precise growth and rigorous adherence to Welding Procedure Specs are paramount for supporting the honesty of bonded frameworks, securing versus possible dangers, and upholding the track record of manufacture firms for delivering premium services and products.
Key Elements of Welding WPS
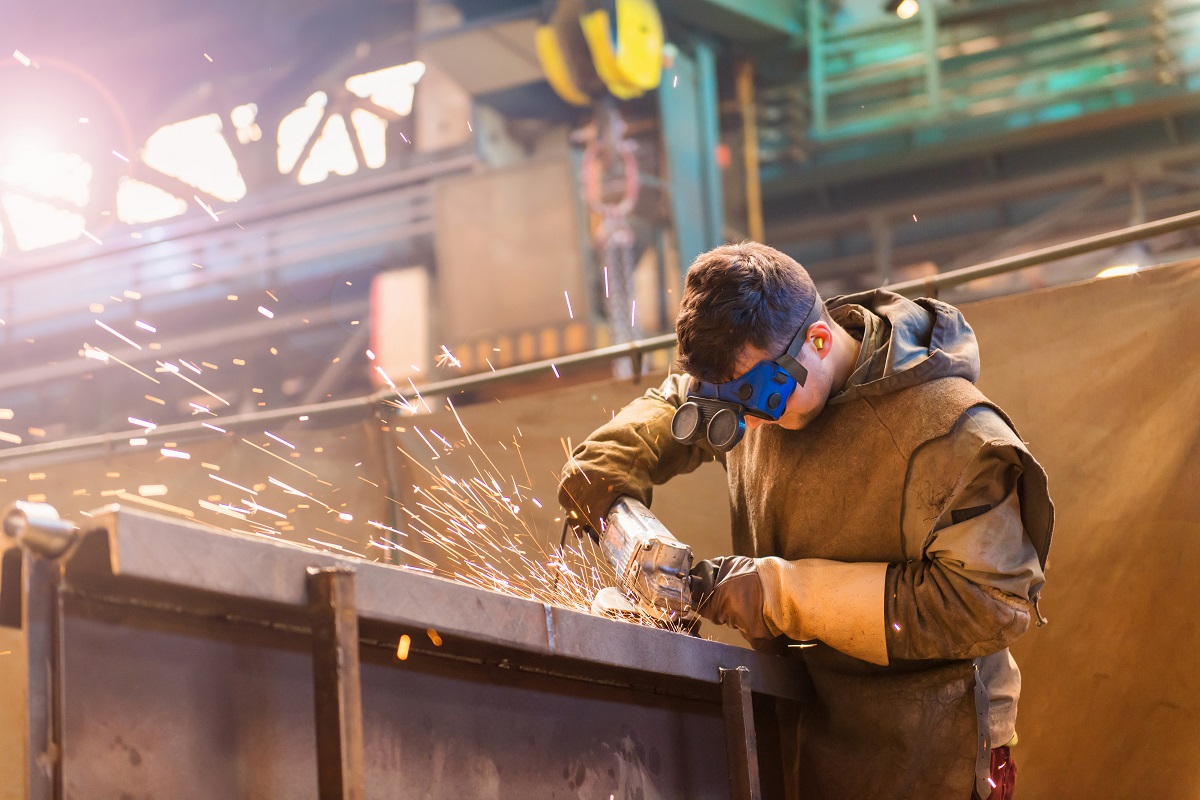
Enhancing Effectiveness With WPS
When enhancing welding operations, leveraging the vital components detailed in Welding Procedure Specifications (WPS) comes to be crucial for taking full advantage of and streamlining procedures efficiency. One means to improve efficiency with WPS is by meticulously choosing the appropriate welding criteria.
Additionally, correct training and qualification of welders in understanding and carrying out WPS can further boost efficiency. Ensuring that all group members are fluent in interpreting and implementing the WPS precisely can remodel and minimize mistakes, conserving both time and resources. Regularly examining and updating the WPS to include any lessons discovered or technological innovations can also add to effectiveness enhancements in welding operations. By accepting the standards stated in the WPS and continually seeking methods to maximize processes, producers can attain higher performance levels and remarkable end outcomes.
Ensuring Safety And Security in Fabrication
Guaranteeing safety and security in construction includes a diverse strategy that includes various facets of the welding process. Welders have to be geared up with appropriate gear such as helmets, gloves, and safety garments to mitigate threats linked with welding activities.
Furthermore, adherence to proper ventilation and fume removal systems is essential in maintaining a healthy and balanced workplace. Welding fumes contain her comment is here dangerous substances that, if breathed in, can pose severe health dangers. Applying effective air flow procedures helps to minimize direct exposure to these unsafe fumes, promoting breathing wellness among workers.
Normal equipment maintenance and evaluations are additionally crucial for guaranteeing safety and security in construction. Faulty machinery can cause crashes and injuries, underscoring the relevance of prompt repairs and routine checks. By prioritizing precaution and cultivating a culture of awareness, fabrication facilities can produce a safe and secure and productive workplace for their employees.
Implementing WPS Best Practices
To boost operational performance and guarantee top quality outcomes in construction processes, incorporating Welding Treatment Spec (WPS) best methods is paramount. Choosing the ideal welding process, filler product, and preheat temperature specified in the WPS is important for accomplishing the desired weld high quality. Ensuring that qualified welders with the needed qualifications bring out the welding treatments according to the WPS standards is important for uniformity and reliability.
Conclusion
Finally, welding WPS plays an essential function in making certain effectiveness and security in manufacture processes. By concentrating on crucial elements, improving effectiveness, and applying best practices, business can enhance their welding procedures. It is essential to prioritize precaution to stop accidents and guarantee a smooth manufacturing procedure. By adhering to these approaches, businesses can unlock the complete capacity of welding WPS in their manufacture procedures.
In the world of manufacture, Welding Treatment Specs (WPS) stand as the backbone of welding operations, determining the needed steps for attaining both click this site performance and security in the construction procedure. By defining vital specifications such as welding processes, materials, joint designs, preheat temperature levels, interpass temperature levels, filler steels, and post-weld warm treatment requirements, WPS provide a standard approach to welding that enhances performance, top quality, and security in construction processes.

When optimizing welding procedures, leveraging the crucial elements detailed in Welding Treatment Specifications (WPS) becomes necessary for streamlining processes and optimizing performance. (welding WPS)
Comments on “Welding WPS Explained: Trick Elements and Conveniences for Your Welding Procedures”